If you are responsible for designing or managing work environments, now is a critical time for you to understand the meaning of a transition to a Circular Economy.
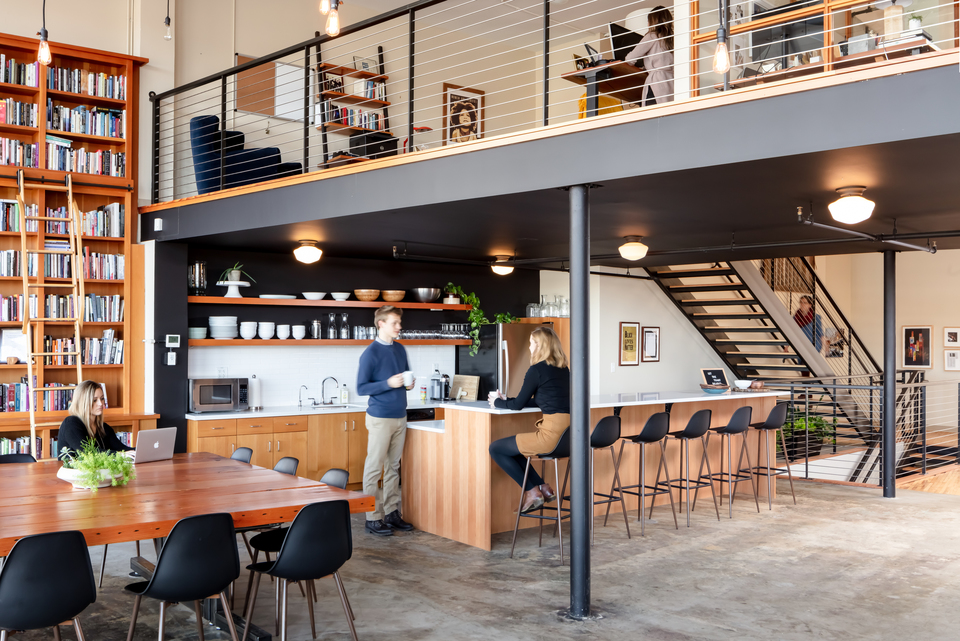
Imagine if all built environment projects eliminated waste, preserved the value of materials and restored natural ecosystems. If you are responsible for designing or managing work environments, now is a critical time for you to understand what the transition to a Circular Economy could mean for your business and the role you play in overall value creation. Design stage decisions have major consequences for managing buildings-in-use and post-use recovery of materials. Those who seize this opportunity will be heroes for achieving sustainability commitments that are targeted for 2030 and beyond.
According to the Ellen MacArthur Foundation, a circular economy is based on the principles of designing out waste and pollution, keeping products and materials in use, and regenerating natural systems. Compared to a linear economy of “take-make-waste,” a circular economy is based on “reduce-reuse-recover” strategies for materials in closed-loop systems. In a linear economy, resources are taken from the ground to make products which are used until no longer needed, at which point they are discarded — i.e., “thrown away.” The circular economy, however, acknowledges that there is no place on our planet called “away” to responsibly dispose of these products. Thus, in a circular economy, products and services are designed with materials that are upcycled or recycled at the end of their useful life.
Compared to a linear economy of “take-make-waste,” a circular economy is based on “reduce-reuse-recover” strategies for materials in closed-loop systems.
Corporations are heeding the call from their stakeholders for greater transparency and accountability in sustainability reporting. Many are hiring Chief Sustainability Officers whose job is to oversee enterprise-level sustainability efforts and communicate progress on all related initiatives with all stakeholders. The expectations of investors, customers, employees and communities are rising. And so is the pressure on Chief Sustainability Officers and Chief Financial Officers to integrate their annual reporting on progress being made in reducing the entire carbon footprint of their supply chains and operations. We anticipate that these sustainable brands will expect an equivalent level of certifications and declarations for healthier workplaces and the well-being of all people who use them. This will become the new normal.
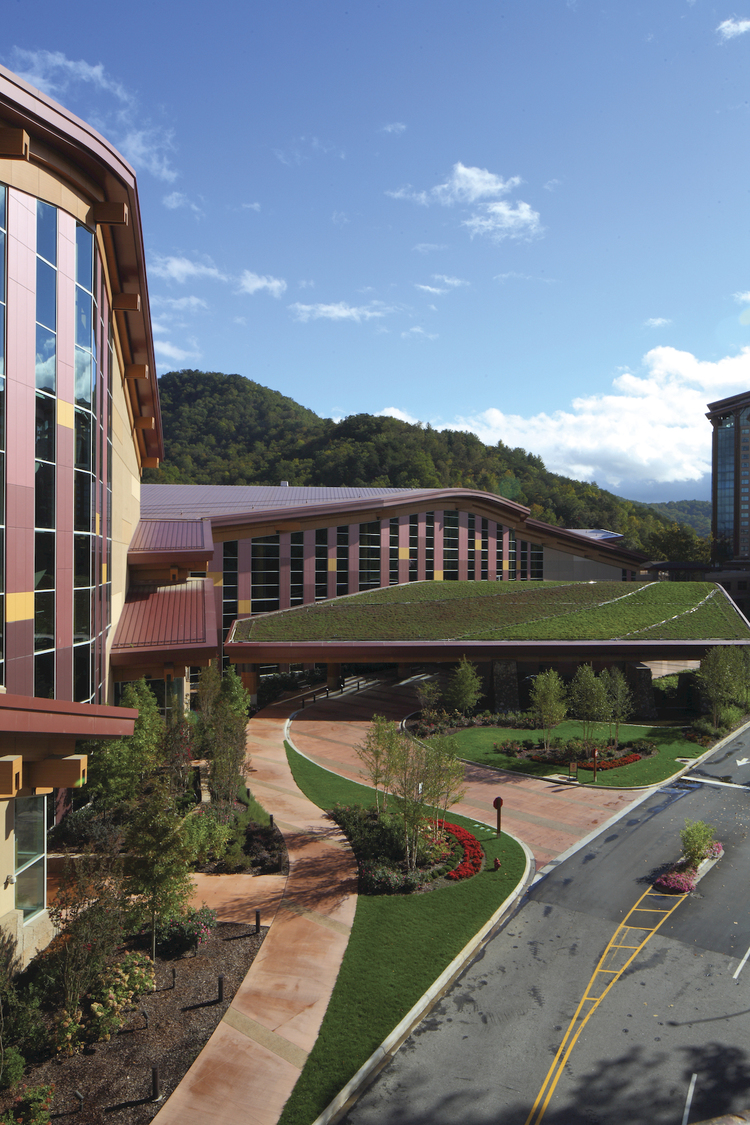
Understanding this new normal required that we address three key questions:
- How would a Circular Economy impact the built environment industry?
- What are its implications for the practice of architecture, engineering and construction (AEC) and workplace management?
- What opportunities does it present to develop new products and services?
Can you believe these statistics and observations attributable to the built environment?
- 39 percent of global carbon emissions are from buildings and construction
- 11 percent from the building materials and construction process itself, and
- An additional 28 percent from building operations.
- Beyond emissions, 40 percent of solid waste finding its way to landfills is attributable to construction and demolition activities.
- Projects that rely upon non-renewable sources of energy and specify carbon-intensive raw materials that are not easily reusable, are still eligible to achieve high scores of widely accepted certification rating systems.
- Conventional “life-cycle analysis” does not account for total costs from a value-cycle perspective that must include restoration of ecosystem services.
The aim of Architecture 2030 to achieve a carbon-neutral built environment by 2040 will require achieving zero carbon emissions from new buildings, existing buildings and embodied carbon. If we are to meet this challenge, no single industry player can solve this alone. It will require systemic improvements to the industry ecosystem and realignment of key working relationships, beginning with the role and responsibility of designers to accelerate circularity as a strategic imperative.
Integrating economy, ecology, and equity as strategic elements begins with shifting from a linear mindset of “take-make-waste” to do more in a circular manner of “reduce-reuse-recover.” To assist project teams in making this shift, we have developed an interactive tool applying circular economy principles and business models. It guides project teams to consider circular strategies throughout all stages in the value cycle of buildings and materials.
Our interactive tool identifies a total of thirty circular strategies. Many of these have already been practically applied in real-world projects, while others remain to be demonstrated. To organize the strategies, we developed an easy to understand framework that we diagrammed as a continuous cycle with four stages of intervention:
- Resource Exchange
- Design and Deliver
- Intelligent Built Environment
- End of Design Life
These four stages are introduced briefly below before we describe the workings of the interactive tool.
Resource Exchange
This tool itself is part of resource exchange. This is where the project team learns about new strategies and finds all the information and materials to then design the built environment. This is the pool of resources, tangible and intangible. A strategy example at this stage is the concept and documentation of a unique material passport. Such a document would carry all information about authentic sourcing, original specifications and previous usage or its passage over time from one building to another. This strategy is related to the concept of buildings as material banks holding resources deposited for a specific service life with value maintained at its highest level for alternative uses in the future.
Design and Deliver
This is the most impactful stage for creating a circular journey in the built environment. Working off the Circular Economy pillar of “Design out Waste,” this phase is where the project team identifies and coordinates the tangible strategies to be applied in the design solution. A strategy example at this stage is Demountable Design. This strategy would prompt the project team to think in terms of considering both constructability at the present stage and disassembly at a future stage when reverse logistics may be deployed, keeping biological and technological material flows in separate closed-loop systems.
Intelligent Built Environment
During this stage, all applied strategies are implemented and tracked as a building-in-use. The project team is now managing the built solution to its optimum potential based on real-time monitoring of actual building systems performance. This is where the project team and occupants would see the third Circular Economy principle of “regenerate natural systems” at work. A strategy example at this stage is IoT / BIM for Operations. This strategy would prompt the project/client team to consider how Internet of Things and Building Information Modeling could be applied through a network of sensors that continuously monitor actual utilization of energy, space, user comfort and other resources, including automated maintenance and repair work orders to keep materials in use longer. In effect, this could create a digital twin of a real environment to optimize performance such as cleaning water and purifying air.
End of Design Life
The follow through, with an emphasis on another Circular Economy principle of “Keep Materials in Use”. This stage is where materials find their way back to being exchanged or headed to their next life for reuse. A strategy example at this stage is upcycling also emphasizing that recycling would be the closed-loop of last resort. Upcycling would involve the project teams in conversations with manufacturers and contractors who willingly take back their product and its materials possibly without the building owner ever purchasing or taking ownership of the product. This strategy provides incentives for the manufacturer to produce a higher quality product that can be repaired and reused. Current examples of this product-as-a-service business model include carpet tile flooring, lighting systems and entire building envelope facades.
Using this framework, our tool provides a simple interface that defines, explains, and connects these stages, strategies and applications. First, the user chooses the value cycle stage of the project:
This choice offers up several strategies to consider during this stage:
Once a strategy is selected, the user will see a definition and application. This will include where the strategy should be addressed or applied related to other stages, in a simple, color-coded format:
In addition, we are developing a virtual library of resources and information for a deeper dive into each strategy. An interactive, beta version of the tool can be accessed here.
Looking Ahead
There is increasing momentum for a Circular Economy across all industries from food to fashion to finance. Now is the time to implement Circular Economy business models and principles in the built environment industry. The expanding role of workplace professionals will become that of a true partner to clients in achieving their 2030 sustainability commitments and adding brand value to their reputations as corporate citizens. We are on a mission to accelerate this transition toward circularity and we welcome others to join us as allies in this quest for a better future.