Material Bank powers complex searches across hundreds of manufacturers and thousands of materials in seconds, turning hours of work into minutes.
The end of this article includes Material Bank’s COVID-19 response from March 30, 2020.

Having launched in January 2019 and introduced at NeoCon in June, Material Bank was heralded as a game changer for designers. I had the opportunity to see for myself on a visit to Chicago, and spent some time with a Material Bank specialist at theMart. What was most impressive were the features that were not immediately evident, the logic and precision with how the concept is executed behind the glossy interior of the Material Bank space. The hands-on experience was not only intuitive and fun to play with all the tools – it gave pause for a bit of nostalgia for the design libraries of the past. Any designer of a certain vintage will most likely have had the pleasure of being tasked with keeping their firm’s design library up to date, a job usually assigned early in one’s career!
We were able to connect with Adam Sandow, CEO of SANDOW in order to find out more on the development of the Material Bank concept and his assessment of how Material Bank is upending the specification process for the A&D community.
WDM: What was the a-ha moment to bring Material Bank to life?
Adam Sandow: SANDOW’s foundation may be in media, but we’ve built a robust, diversified business that includes tools, services, and solutions that complement our media properties.
After SANDOW acquired Interior Design and Material ConneXion and became fully immersed in the A&D industry, we noticed the massive inefficiencies of the sampling process. Designers were spending a ridiculous amount of time – up to 39 percent of their day searching for and ordering products and materials for their projects. We knew we could reinvent the process and we spent two years studying pain points in the industry from both the designer and manufacturer perspectives in order to build a solution. With Material Bank we have fundamentally changed the speed, process, and search capabilities that material specifiers experience when searching and sampling materials.

Adam is correct in his assessment of where the pain points lie in the materials and furniture specification process. This is especially true when there are limitations of time (based on design fee structure), and space (in design studios), and the time needed to keep a library up to date. Also issues around finding time to meet with product reps and manage the deluge of samples and catalogs can take a big bite out of a designer’s day. What Material Bank has done is to streamline the process with a platform that is easily accessible from multiple devices and allows the designer to play with colors and materials quickly and get the physical samples in short order (next day).
WDM: How did you socialize this to get manufacturers on board?
Adam Sandow: As the publisher of the 87-year-old Interior Design magazine, we have deep relationships and existing credibility with manufacturers, giving us an open door to educate them how the platform would resolve so many of the industry’s inefficiencies. They understand the value proposition and recognized that Material Bank was going to change the industry. Every three days, a new manufacturer joins Material Bank. At this point, we have a backlog of companies who want to be on the platform, and we expect to have between 200 and 250 completely on-boarded by the end of the year.
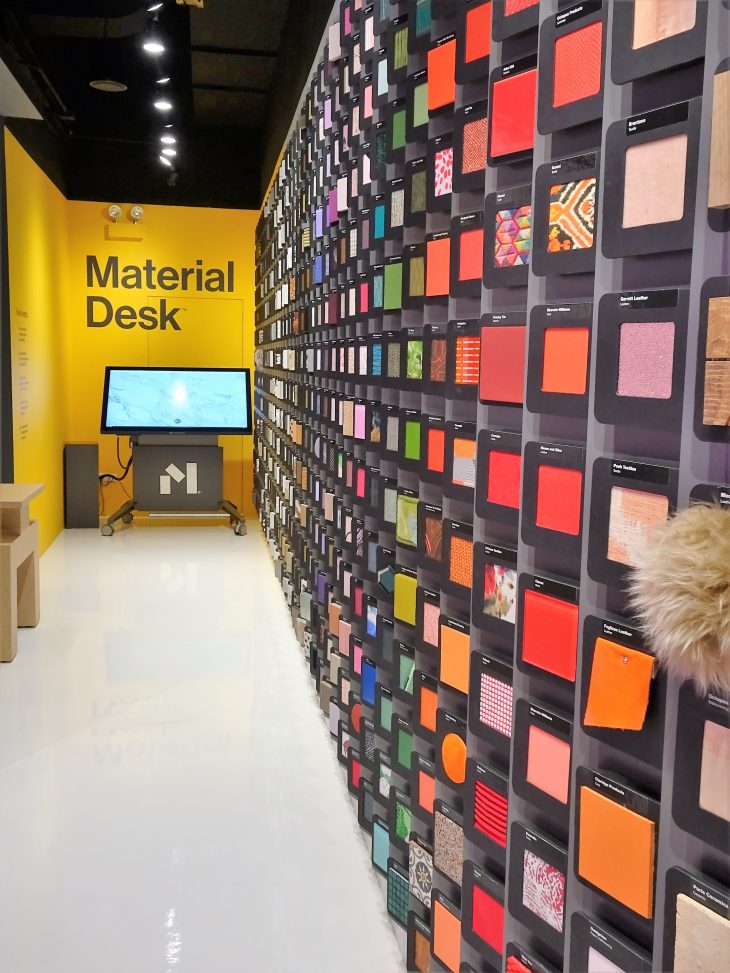
To prove Adam’s point, testing the concept in person was dangerously fun. In the Material Bank space there are multiple ways to experiment with materials and easily develop palettes and material selections. Designers love the tactile experience and there are multiple ways to see different materials throughout the space. What is most interesting (and functional) is the way the samples are displayed and are also married to the technology that drives the Material Bank system. As more manufacturers are added designers will have even more options to work with as they develop design concepts for their clients. Now that the system is established, integrating the new products into the program can only enhance the flexibility and usefulness of this design tool. What is impressive is how the technology takes over once selections are made and a concept comes together and facilitates the ability to collect, ship and get samples in the designer’s hands quickly and efficiently.
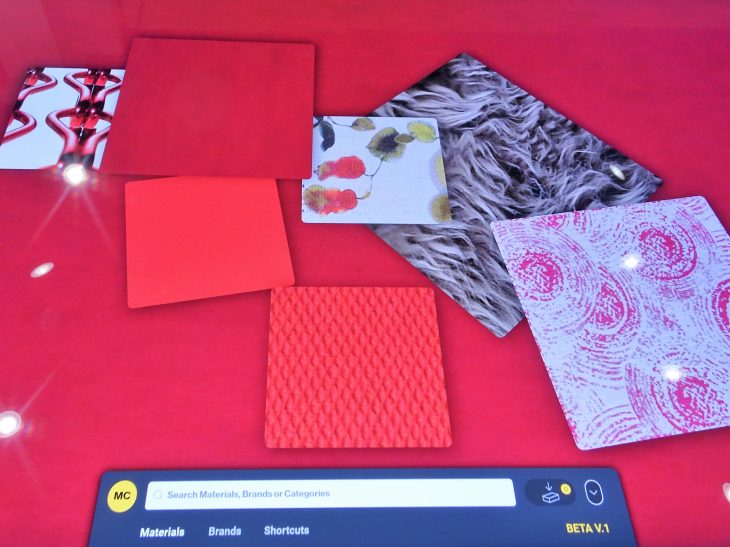
Not sure what you are looking for? There is a solution for that also! The Material Bank team has put together some idea triggers, conveniently located in the wall of drawers adjacent to the Materials Desk. Exploring the contents of that feature is like opening a treasure chest of designer treats – Each suggested scheme has a selection of samples to convey a specific theme or mood.
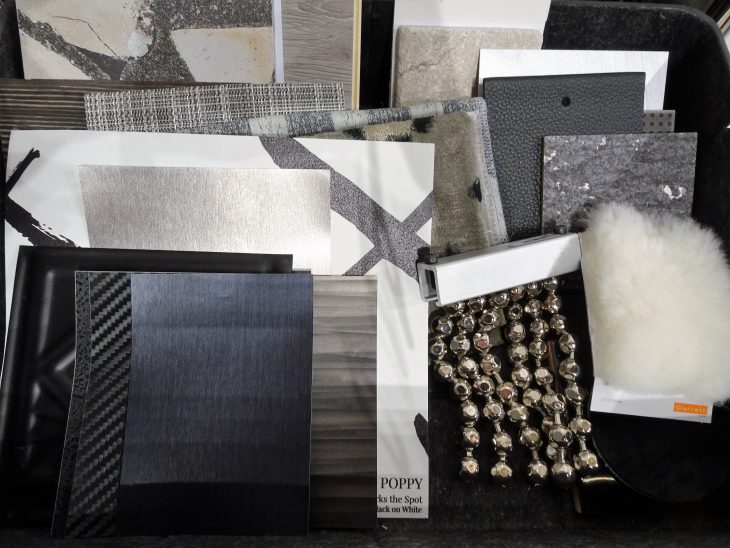
After playing around for a while the specialist explained what happens once a designer makes selections, puts a project board together and orders the samples. The logistics behind this part of the program, were in fact the most interesting part of the story (to me). After going through a traditional material selection effort, think about how much time it would take just to get, let’s say, ten samples. That is ten reps or companies to contact, either phone or online sample request. Then those ten companies, each must pull, package and send the samples. On the receiving end that is ten packages to open, packing materials to deal with, and in the end return or add to the piles of samples in the library! In my testing mode, the Materials Bank folks were kind enough to send a sample box to me, so I could see for myself how things work.
The details on the ordering and shipping process can be found here.

The thought behind the level of detail in planning the logistics behind material bank is considerable. Everything arrives in one box without excess bubble wrap, peanuts and packaging. The packaging is unique in that it unfolds and reconfigures easily so that unused samples can be easily returned. The return label is already on the box.
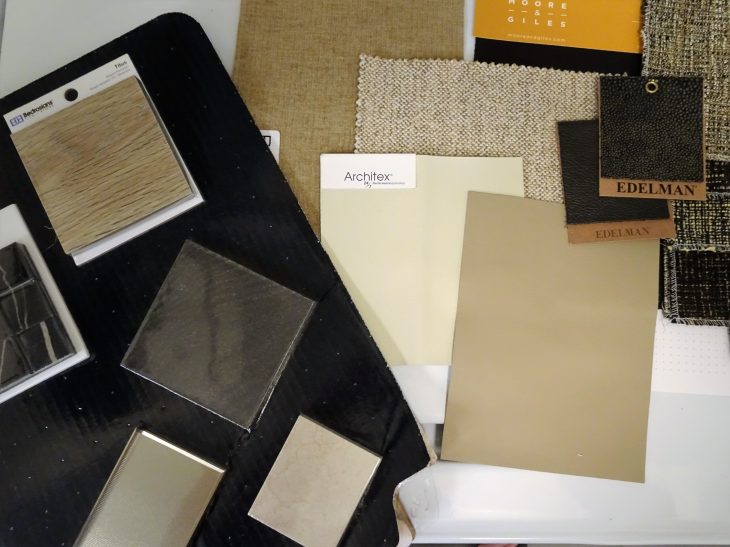
After reviewing how Material Bank works, and experiencing the process firsthand, we had more questions for Adam.
WDM: What are the criteria to join Material Bank? (Credentials, cost, specifiers/designers)?
Adam Sandow: Material Bank is a tool specifically for design professionals and has a comprehensive screening process for approval. Our user support team carefully vets every applicant, researching their credentials and confirming they are indeed specifiers. Material Bank is always free for architects, designers, librarians, purchasing agents and other specifiers.
WDM: What is the biggest surprise in how designers are using the services?
Adam Sandow: Our biggest surprise is how fast Material Bank has been adopted by corporations and end users. We already have eight percent of Fortune 500 companies using Material Bank to discover and source new materials. We have facility managers and government institutions using the platform; everyone from luxury retailers and large quick service restaurants using Material Bank to select products for their projects.
WDM: How has the development of Material Desk going? Have you placed it in any architecture/design firm offices yet?
Adam Sandow: The first Material Desks will go into design firms for beta testing in Q4 with rollouts in 2020. We debuted Material Desk at NeoCon and at our Material Bank Lab and the response was tremendous.
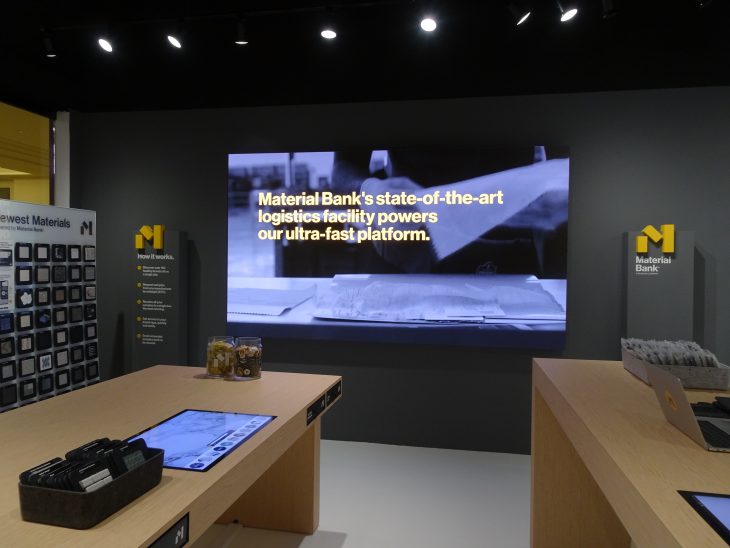
We can understand why the response from the design community is so positive. Finding ways to improve the process of selecting products for a project utilizing technology and improved logistics for materials sampling is a real game changer. I would imagine that accelerating the time to identify products, pull palettes together, investigate options allows more time to craft great design solutions. For sales reps, freeing them from the time consuming task of coordinating sample delivery (and retrieval), and catalog updates will give them more time to connect with designers on introducing new products, fielding questions on lead times and delivery issues, and sharing their company’s research educational offerings. It will be interesting to see what other innovations are in store as Material Bank expands the platform, is embedded in design firms, and expands physical locations in different markets.
Material Bank COVID-19 Response – March 30, 2020
We were able to connect with our friends at Material Bank to find out what they are currently doing to manage in the age of COVID-19. As work has migrated from office to home, this can present a dilemma to designers without access to their material libraries. Here is their response to our questions about how they are working through the challenges presented to their fulfillment center in the face of the current situation:
How are you preparing your front-line employees to manage on a day to day basis?
A summary of our employee education efforts includes:
- We have brought in full-time medical professionals to lead screenings and educate our employees on how to maintain a clean, sanitary workspace.
- All team members will follow a regulated hand washing schedule and be required to wear latex gloves.
What other precautions are you taking at your facilities?
- We are monitoring and restricting access to everyone (managers, staff, guests, and vendors) entering the Logistics Hub.
- Our medical professionals are conducting skilled screenings to ensure no one with a fever or potential exposure to COVID-19, has approved access.
Are there any other things you are doing to safeguard the physical environment in the Logistics Hub?
We have deployed dedicated resources to disinfect the Logistics Hub continually, with full sweeps throughout the day.
What about dealing with most likely increased demand for samples?
We are working with manufacturers to maintain appropriate levels of inventory and continuing to partner with FedEx so we can deliver samples fast and efficiently.
How about managing the packing and shipment issues?
- We have implemented new procedures to ensure we’re delivering materials safely.
- All items, including Sample Returns, received at our Logistics Hub will be quarantined for a seven-day period to rid bacteria and prevent COVID-19 exposure, before being processed through our system for sampling.
- We are also treating all necessary packages with Lysol as an added measure.
What about your employees not based in the Logistics Hub?
Out of abundance of caution, we have asked our member support team to work remotely and eliminate all travel. They will remain fully accessible and operating in accordance with our regular hours.
We are continuously updating this page that lives on our website.
What else to our readers need to know?
In terms of additional ways Material Bank is meeting designers needs through this unprecedented time:
- MB members can change their default address from their office to their home or even send samples directly to clients
- With no/limited FaceTime interaction with brand reps- material discoverability and sampling on our platform is one of the only ways members can do business with brand reps right now
- Design professionals can collaborate with team members on MB boards to continue pushing projects forward.
- Samples Returns have always been an essential part of our commitment to sustainability, and currently, they are more crucial than ever. If COVID-19 brings change to our Brand Partners or the supply chain, we want to take measures to ensure we sustain appropriate levels of inventory.